In the field of electrical engineering, establishing solid connections isn’t just about connecting wires; it’s about creating long-lasting bonds that can withstand the test of time. That’s where HEXWELD comes in – a groundbreaking process that operates at the molecular level, ensuring sturdy and durable connections.
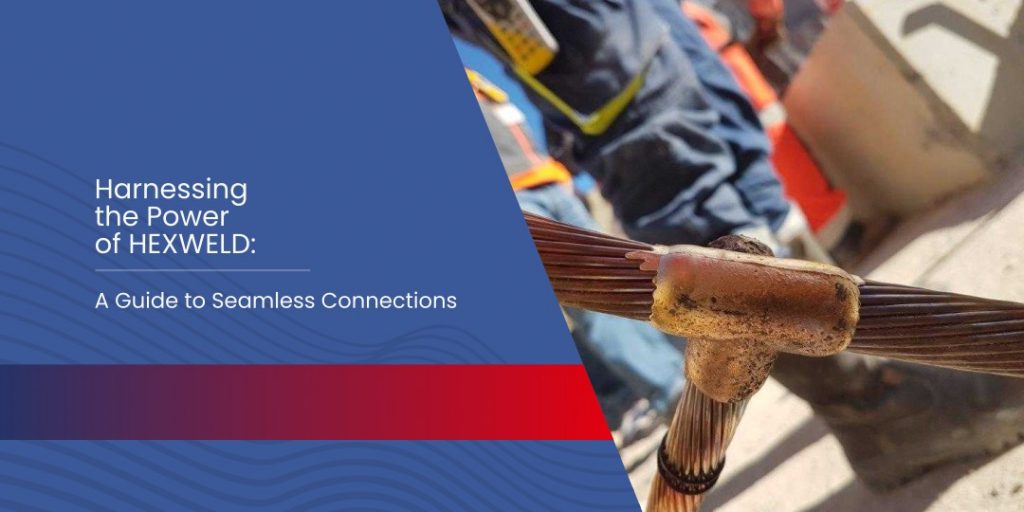
Understanding the HEXWELD Connection
Aluminum can reduce copper oxide, which produces enough heat to melt copper. This process creates a strong bond at the molecular level. A HEXWELD connection uses a graphite mold tailored to specific conductors to ensure the best electrical connections. But what exactly is involved in creating a HEXWELD connection?
- Weld Sleeve: This component extends from the weld body, providing additional mechanical strength where the molecular bond forms.
- Conductor: Refers to the metallic materials that are being welded together.
- Riser: This part is located on top of the weld and handles any excess weld material and slag.
- Weld Body: This is the main area where the welding process occurs – under the tap where conductors are fused.
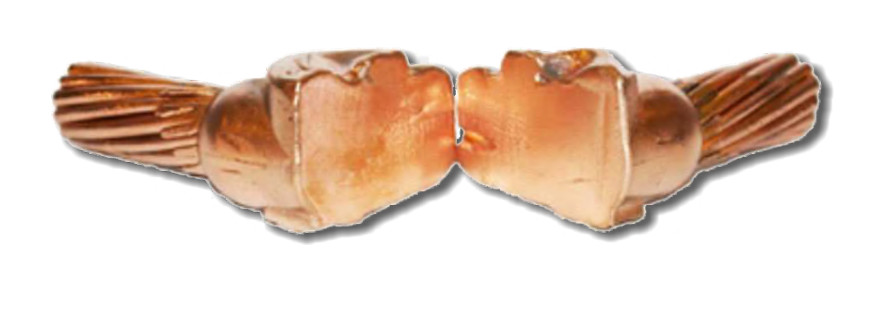
Inspecting HEXWELD Connections
Ensuring the quality of a HEXWELD connection is crucial. Here’s what to look for:
- A solid body weld with a clear cross-section is more significant than the conductors.
- Sleeves should be complete without any slag.
- The riser should show minimal to no signs of contamination.
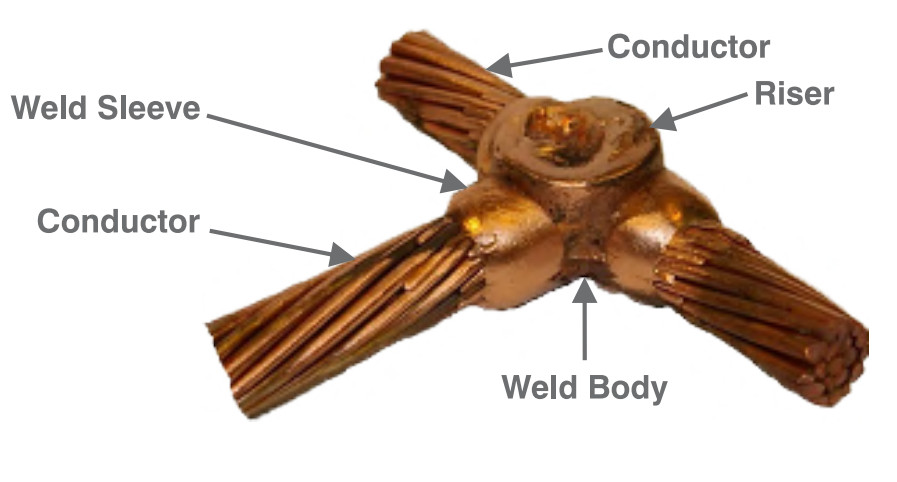
Applications of Exothermic Welding
HEXWELD’s versatility extends across various industries:
- Solar Energy: Enabling efficient power transmission in solar installations.
- Power Plants: Ensuring reliable connections in the heart of energy production.
- Substations: Vital for maintaining grid stability and reliability.
- Rail: Facilitating safe and efficient rail operations.
- Wind Energy: Supporting the expansion of renewable energy sources.
- Telecommunications: Ensuring seamless communication networks.
Inspecting HEXWELD Mould
The maintenance of the mould is just as important as the welding process. It involves several steps such as:
- Regular inspection of conductor openings to prevent leaks.
- Ensuring a well-defined weld cavity free of chips or cracks.
- Checking the tap hole and disk seat for proper functionality.
- Keeping the mold parting surface intact to seal the reaction effectively.
- Safely maintaining the crucible to hold the reaction securely.
Becoming proficient in HEXWELD connections involves more than just mastering the technique. It requires a combination of scientific knowledge, precision, and careful attention. By comprehending the process, thoroughly examining connections, and properly maintaining equipment, we can guarantee that our electrical systems will remain sturdy and dependable for many years. Therefore, let’s take advantage of the strength of HEXWELD and create connections that can withstand any obstacle.